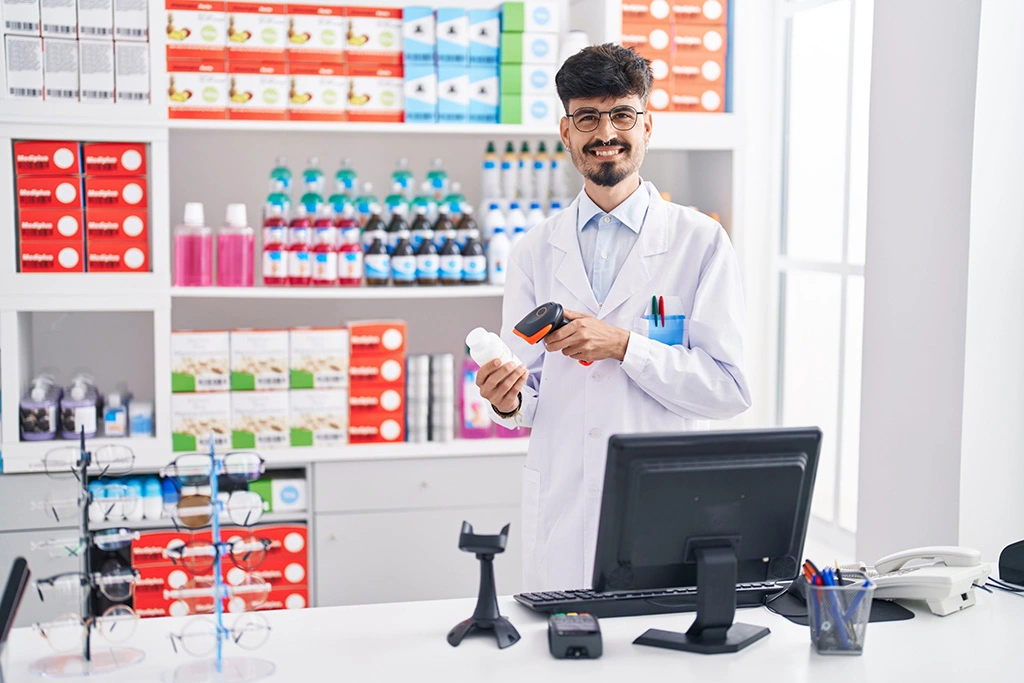
Mar, 01 2023
Implementing a Supply Chain Management ERP for Medical Product Supplier
Abstract
Genmed Shoppes Pvt. Ltd., a leading pharmaceutical distributor, faced challenges in managing its complex supply chain operations across various store types. To address these challenges, the company sought to develop a customized ERP system tailored for their specific needs.

Problem
Supply chain operations involved managing transactions for various entities, including main branches, customers, retailers, wholesalers /distributors, and manufacturers. The company needed an ERP system that could effectively handle these diverse transactions and optimize profit margins. Additionally, manage batch and expiry date-wise items and stock levels.

Solution
To address these challenges, a team of IT professionals was assembled to develop and implement a customized Supply Chain Management ERP system.
The project involved the following steps:
1. Requirements Gathering and Analysis: The project team conducted a series of client meetings to gather detailed requirements for the ERP system. This included understanding the company’s business processes, identifying pain points, and defining key functionalities.
2. System Design and Development: Based on the gathered requirements, the team designed and developed a comprehensive ERP system that incorporated Point of Sale (POS) and financial transaction management capabilities. The system was designed to be flexible and adaptable to accommodate the diverse needs of client’s various store types.
3. Data Migration and Integration: The team carefully migrated existing data from legacy systems into the new ERP system. This ensured data integrity and consistency across the organization.
4. Testing and Deployment: The ERP system underwent rigorous testing to ensure functionality, performance, and security. Once testing was complete, the system was deployed to the production environment.
5. Training and Support: The team provided comprehensive training to client’s employees on how to use the new ERP system. Ongoing support was also provided to ensure a smooth transition

Result
1. Improved Transaction Management: The system streamlined and automated transaction processing, leading to reduced errors, improved efficiency, and increased productivity.
2. Optimized Profit Margins: The system provided real-time insights into profit margins, enabling the company to make informed decisions to optimize pricing and maximize profitability.
3. Enhanced Inventory Management: The system provided accurate and real-time visibility into inventory levels, reducing stock outs and overstocking, and ensuring optimal stock levels.
4. Streamlined Batch and Expiry Management: The system effectively managed batch and expiry date-wise items, ensuring compliance with regulatory requirements and minimizing product waste.
5. Improved Collaboration and Communication: The system facilitated better collaboration and communication between various departments within the Genmed Shoppes Pvt. Ltd., as well as with external suppliers and customers.
Conclusion
The development and implementation of a customized Supply Chain Management ERP system proved to be a resounding success for Genmed Shoppes Pvt. Ltd. The system addressed the company’s unique challenges, streamlined operations, and optimized profit margins. The project demonstrates the power of technology in transforming supply chain management processes and achieving operational excellence.
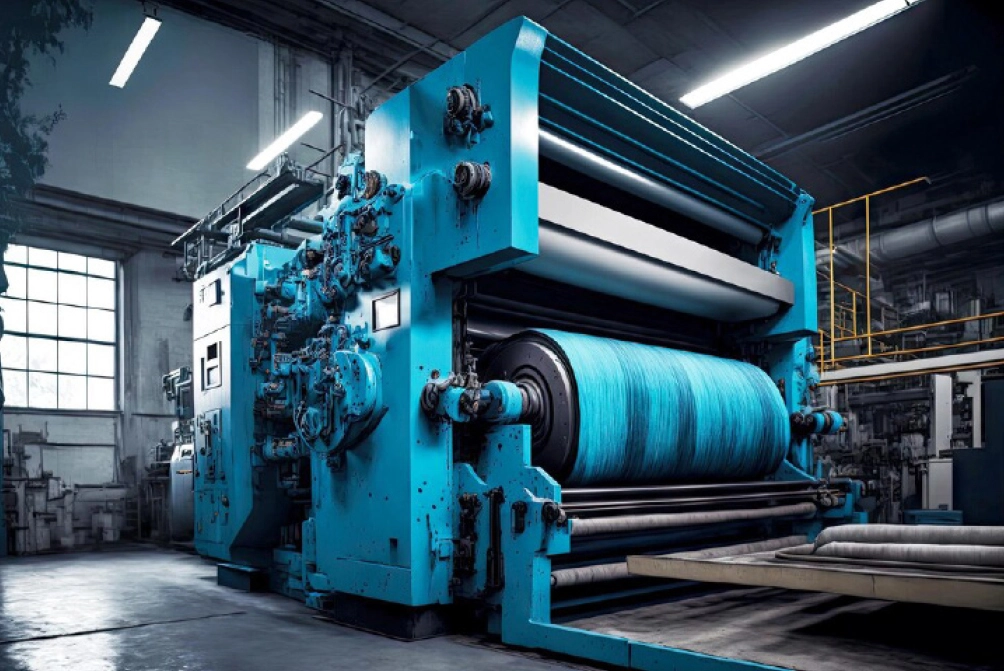
Feb, 01 2023
Transforming Dyeing Operations with TexPro ERP
Overview
In the competitive dyeing industry, efficiency and precision are paramount. Manual, paper-based systems often lead to delays, errors, and a lack of real-time insights, hindering production optimization and profitability. To address these challenges, a leading dyeingcompany sought to implement TexPro, an ERP system specifically designed for the dyeing industry.

Challenge
The company faced challenges with its manual, paper-based system, including limited traceability, inefficient program management, a lack of real-time monitoring, inconsistent recipe management, and manual process oversight. These issues hindered production efficiency, decision-making, and transparency.

Solution
To address these challenges, the company implemented TexPro, an ERP system tailored for the dyeing industry.
TexPro offered several modules that addressed the company’s specific needs:
1. Lot Tracking Optimization: TexPro’s dynamic lot register enabled real-time tracking of lot movements, providing a high level of traceability.
2. Program Registry Enhancement: TexPro streamlined party program creation and management, allowing real-time tracking of program statuses.
3. Advanced Chart Management: TexPro auto-generated essential reports, including batch slips, chart forms, and chart recipes, providing detailed batch progress monitoring.
4. Recipe Governance Streamlining: TexPro organized recipes systematically based on parties and quality criteria, ensuring consistency in the production process.
5. Process Oversight Augmentation: TexPro’s dedicated mobile application enabled real-time batch monitoring and swiping, enhancing process oversight.
6. Utility Refinement: TexPro provided multi-department, multi-user access, instant chart process tracking, secure data handling, and mobile alerts for batch anomalies.
7. Exhaustive Analytical Reporting: TexPro offered comprehensive reporting, including costing, production, machine-wise, re-process batch, and dispatch reports.

Result
The implementation of TexPro ERP resulted in significant benefits for the dyeing company, including:
1. Enhanced Traceability: Improved lot tracking facilitated better identification of production bottlenecks and streamlined process troubleshooting.
2. Efficient Program Management: Streamlined party program creation and management reduced time consumption and errors, improving operational efficiency.
3. Real-time Monitoring and Decision-making: Real-time visibility into batch progress and machine performance enabled timely decision-making to optimize production and address potential issues promptly.
4. Consistent Recipe Management: Systematic recipe organization ensured consistency in the production process, reducing the risk of errors and product inconsistencies.
5. Enhanced Process Oversight: Mobile-enabled real-time batch monitoring and swiping improved process oversight and transparency.
6.Data-Driven Decision-making: Comprehensive reporting provided valuable insights into production costs, efficiency, machine performance, and re-process opportunities, enabling data-driven decision-making.
Conclusion
TexPro ERP transformed the dyeing company, optimizing operations, enhancing traceability, and boosting profitability in the industry.
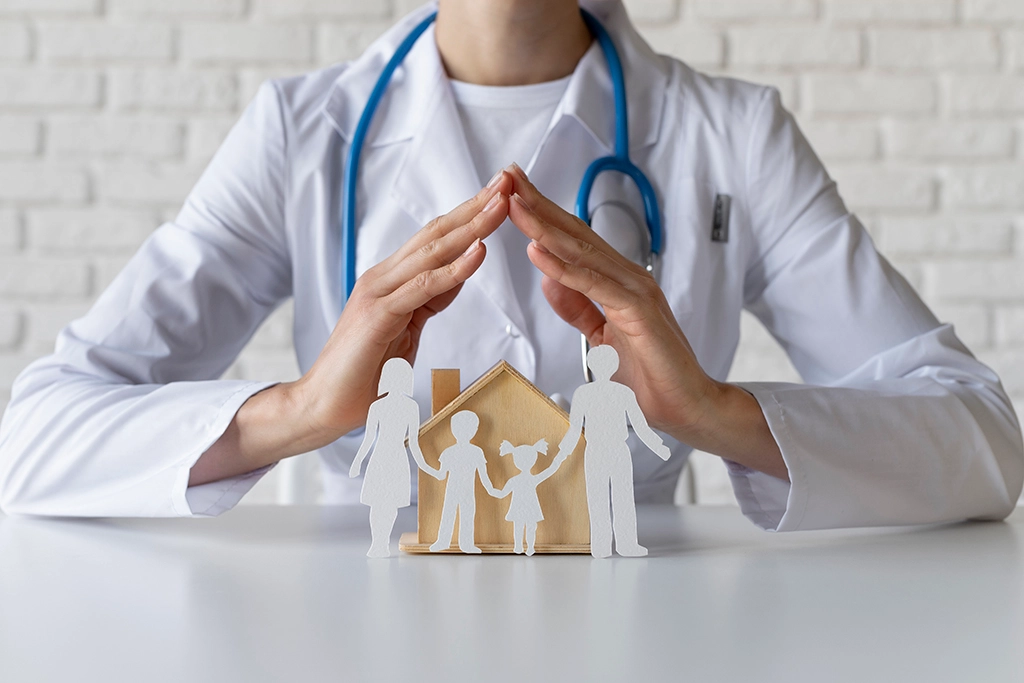
Jul, 24 2021
Streamlining Healthcare Claims Processing with EDI
Overview
In the healthcare industry, efficient and secure claims processing is crucial for ensuring timely reimbursement and maintaining financial stability. Manual claims processing, however, is often time consuming, error-prone, and susceptible to compliance issues. To address these challenges, a leading healthcare organization sought to automate claims processing using EDI (Electronic Data Interchange), adhering to HIPAA (Health Insurance Portability and Accountability Act) and ANSI X12 standards.

Challenge
Manual data entry caused delays in claims processing, impacting reimbursement timelines. This method also increased the risk of errors and non-compliance with HIPAA regulations. Additionally, the lack of real-time visibility into claims status hindered issue resolution and fraud detection.

Solution
To address these challenges, the organization embarked on a twoyear project to implement EDI automation using OopFactory, a leading healthcare software solution.
The project involved the following steps:
1. Requirements Gathering and Analysis: The project team conducted a comprehensive analysis of existing business applications and processes to gather end-user requirements and identify areas for improvement.
2. EDI Standards Implementation: The team implemented ANSI-based Claim 837P, Eligibility, and E-prescription concepts, ensuring adherence to HIPAA and EDI ANSI standards.
3. Database Development: Relational databases were created to store and manage healthcare data. SQL queries and stored procedures were developed for data validation, extraction, ad-hoc data analysis, testing, report generation, and ETL load jobs.
4. Efficient EDI Transaction Management: Configured system for seamless submission of transactions to payers and clearinghouses, adeptly handling responses and errors.
5. eMedNY Integration: The project facilitated the submission of single and batch requests of EDI files to the eMedNY clearinghouse,retrieving responses using SOAP API.
6. Coding Standards Integration: ICD10, SNOMED-CT, LOINC, and HCPCS codes were incorporated into the project to enhance code integration and ensure accurate claims processing.
7. EDI Documentation: Comprehensive documentation was developed related to EDI processes, mapping, and trading partner configurations to ensure consistent and reliable operations.
8. Compliance Management: Strict compliance with EDI standards, protocols, and regulations was maintained to guarantee data integrity, security, and regulatory adherence.

Result
Healthcare EDI implementation led to:
1.Efficient Claims Processing: Automated processing accelerated reimbursement and improved cash flow.
2. Error Reduction and Compliance: Automated validation minimized errors and ensured HIPAA compliance.
3. Real-time Monitoring and Decision-making: Real-time visibility into batch progress and machine performance enabled timely decision-making to optimize production and address potential issues promptly.
4. Real-time Claims Visibility: Immediate status updates prevented delays and fraud.
5. Enhanced Analytics: Automated data analysis provided valuable insights for informed decisionmaking, boosting efficiency and reducing costs.
Conclusion
EDI automation revolutionized healthcare operations, boosting efficiency, accuracy, compliance, and data visibility. This technology-driven project showcases its transformative impact on financial management.